Welding technology plays an extremely important role in the assembly of electronic products. General welding is divided into two categories: one is mainly applied to the welding of through-hole plug-type electronic components and printed boards - wave soldering, the so-called wave soldering (wavesoldering) is to melt the solder, the electric The pump or electromagnetic pump sprays the solder wave peaks required by the design to allow the printed boards pre-equipped with electronic components to pass through the solder peaks to achieve the mechanical and electrical connection between the component terminals or the leads and the PCB pads. Brazing; the other is mainly used for surface-mount components and printed board reflow soldering (reflowsoldering), also known as reflow soldering, the so-called reflow is re-melted by pre-distribution to the PCB pad The paste solder on the solder paste realizes the soldering of the surface-mount components or the mechanical and electrical connection between the leads and the printed circuit board pad, thereby realizing the circuit function with certain reliability. With the large-scale use of surface mount components in electronic products, reflow soldering technology has become a major process technology in surface mount technology. Its main process features are: the surface of the metal to be welded is cleaned (removed oxide) with a flux to make it have good wettability to the solder; the molten solder is supplied to moisten the metal surface; and the intermetallic compound is formed between the solder and the weld metal In addition, micro-welding can be realized.
Reflow soldering is a group or point-by-point soldering process in which a proper amount and appropriate form of solder are applied to the soldered area (pad) of the PCB in advance, and then the surface mounted components are placed and the solder is reflowed by the external heat source to meet the soldering requirements. Reflow soldering has the following features compared to wave soldering:
1. Reflow does not require the components to be directly immersed in the molten solder as in wave soldering, so the thermal shock to the components is small;
2. Reflow solder is only applied to the desired area, which greatly saves the use of solder.
3, reflow can control the amount of solder to discharge, to avoid bridging and other defects;
4. When the component placement position deviates by a certain amount, due to the surface tension of the molten solder, as long as the solder is applied in the correct position, the reflow soldering can automatically correct this minor deviation during welding, so that the component is fixed in the correct position;
5, can use local heating heat source, which can be on the same substrate with a different reflow soldering process welding;
6. Impurities are generally not mixed in the solder, and the solder composition can be properly maintained when solder paste is used for reflow soldering.
Our main business includes: SMT machine, Printer Machine, SMT Cleaning Machine, PCB Separator and Mounting Pick Machine, if there is any need, please contact us.
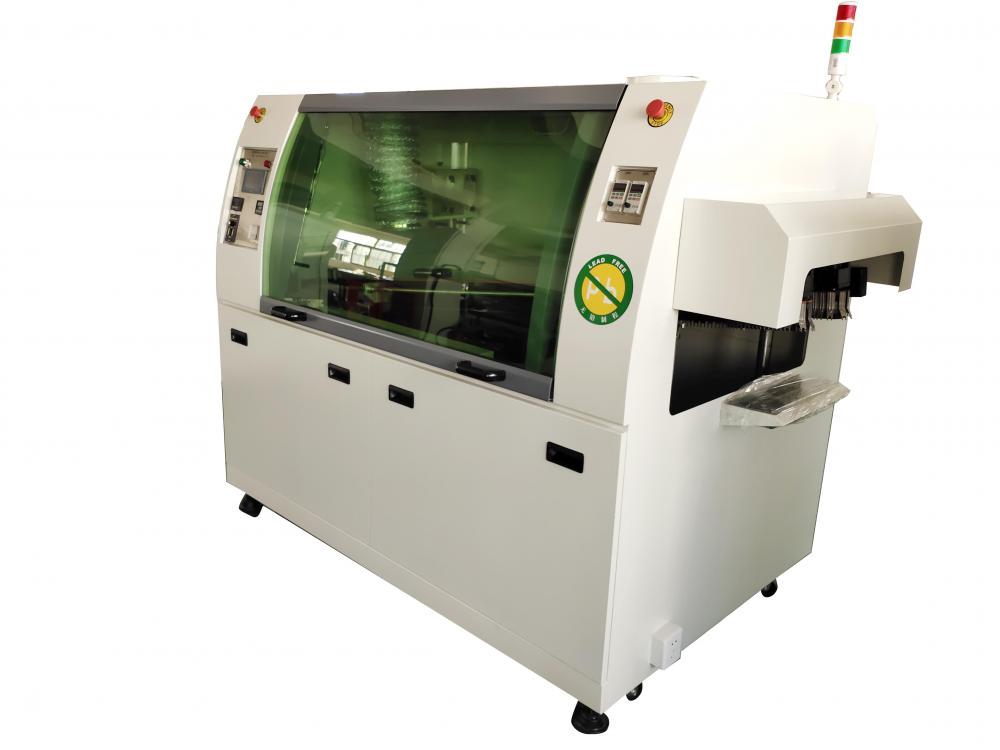